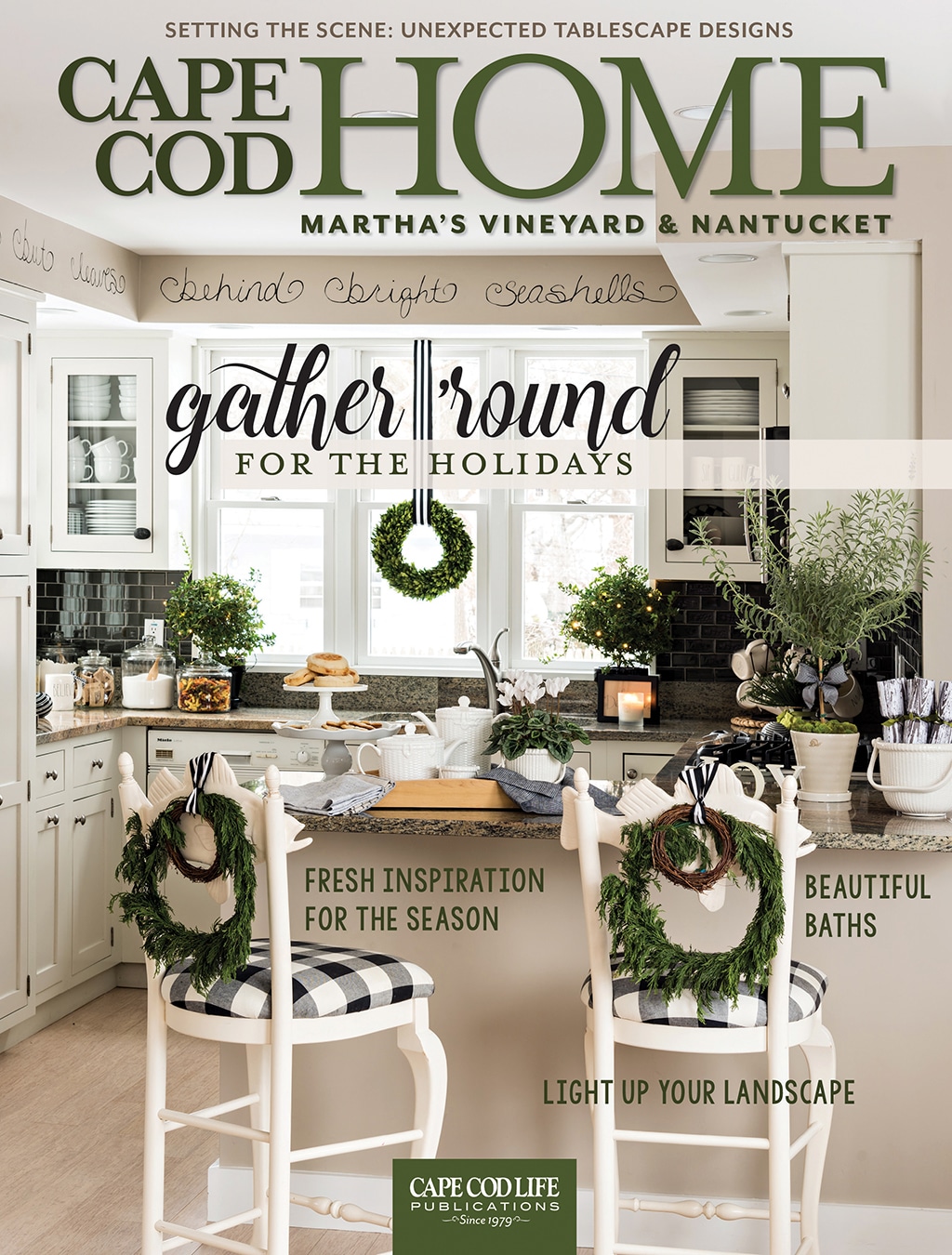
A Sign of the Times
Cape Cod Home / Winter 2018 / Home, Garden & Design, People & Businesses
Writer: Ellen Albanese
A Sign of the Times
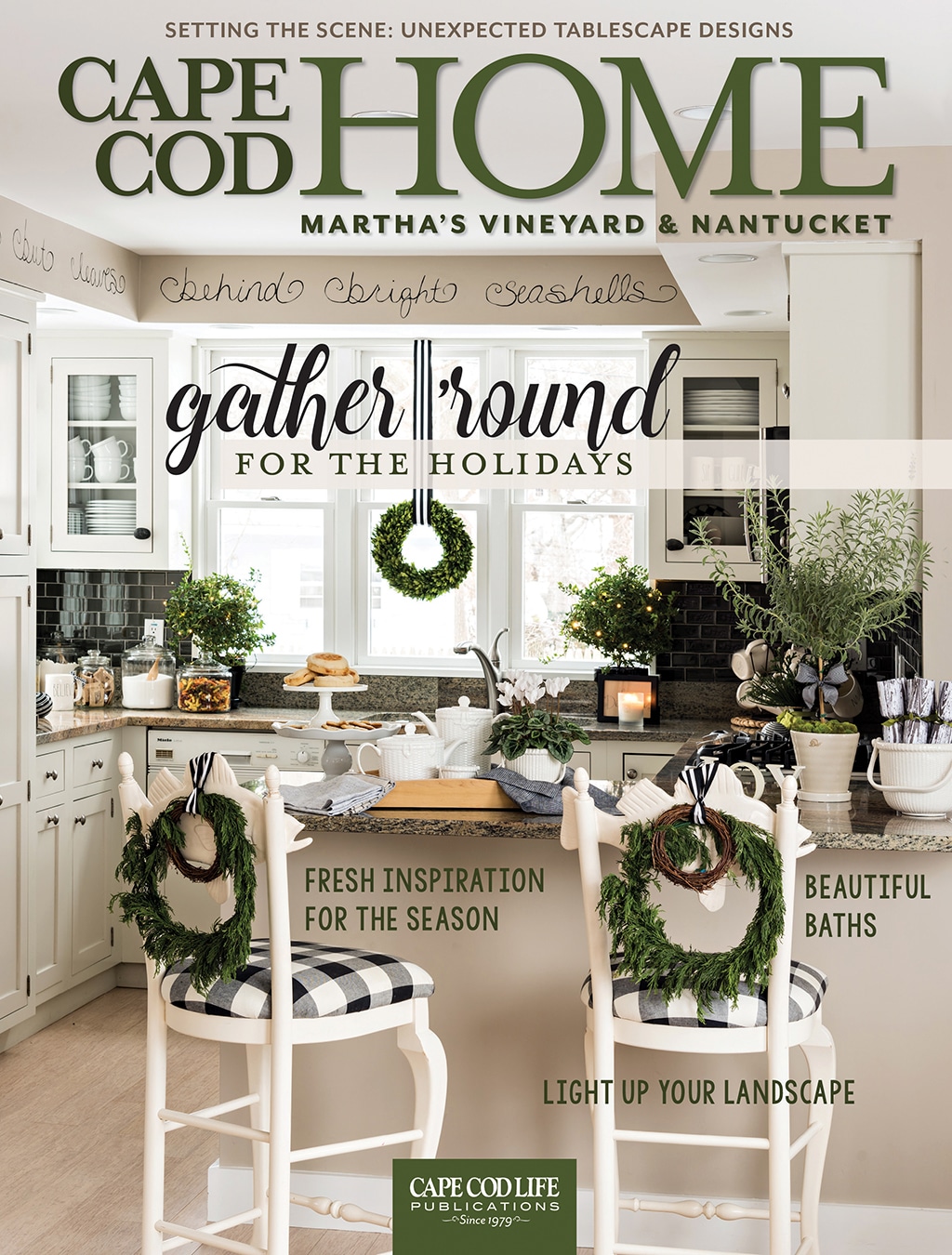
Cape Cod Home / Winter 2018 / Home, Garden & Design, People & Businesses
Writer: Ellen Albanese
Cape & Islands artisans keep the tradition of quarterboards alive
Photos courtesy of Dan Driscoll
Once used to identify sailing ships, quarterboards have evolved into a distinctive form of home décor that recalls Cape Cod’s seafaring heritage. Today these ornamental signs are most often found above the main entrance to a home or garage, with lettering that spells the family name or a clever slogan. Decorative carved end pieces—such as scallop shells, pineapples or whales—complete the custom look.
After the War of 1812, many privateers became pirates, explains Paul McCarthy of Nantucket Carving and Folk Art. To protect legitimate ships, the government required all ships to have signage on the aft quarter of the vessel. It typically fell to the ship’s figurehead carver to make the “quarterboards.”
Because of the treacherous shoals around Cape Cod and the Islands, shipwrecks were common during the heyday of the maritime trade, from around 1850 to the 1930s. “The quarterboards collected from wrecked ships were huge—perhaps eight to ten feet long and appropriate to the scale of the ship,” writes Sharon Hubbard in “Quarterboards: A Unique Art Form” (Mill Hill Press, 2008). “Due to their size and shape, the most likely place to store them was on the wall of a house or barn.”
McCarthy has been hand carving quarterboards for 50 years and figures he’s produced about 9,000 signs in that time. His business partner, Jean Petty, an expert in color matching, does all of the time-consuming finish work along with complete restorations of old pieces. While quarterboards were originally sized to the scale of a ship, today they are sized to the scale of trim boards on a typical house, he says. Since most trim boards are 5.5 inches, the typical quarterboard is 4.5 inches high. The length is determined by the amount of text to be carved onto the board. “Some people start giving me encyclopedias for these quarterboards,” he says with a laugh, but most are around 4 feet long.
White pine is the traditional wood. During the height of the maritime trade, most timber went into the building of ships, McCarthy says. What was left over was Eastern white pine—accessible, plentiful, and big—which was used for figureheads and other ornamentation. It’s still McCarthy’s favorite wood. “I use the grain to my advantage,” he says. “I can see it; I know what it’s doing.”
Another traditional material is gold leaf. In addition to increasing visibility, gold leaf was used for its durability, McCarthy says, pointing out that it’s the same metal used on the domes of churches and public buildings. “When you see a quarterboard with gold on it, you recognize it. It’s startling. It’s stunning.” Because of the high price of gold today, McCarthy has been using gold leaf more on ornamental ends than on individual letters.
Shells, whales and pineapples are among the most popular designs for the ornamental ends, which in McCarthy’s studio are carved into the board itself, not applied separately. Using pineapples as symbols of hospitality goes all the way back to Nantucket’s whaling days. When whaling ships visited the Hawaiian Islands, the sailors would gather pineapples and store them in the ship’s hold. When the ship returned, the captain would set a pineapple on an iron fence post in front of his home to let islanders know the ship and crew were back and everyone was invited to stop in to celebrate.
Prices depend on size and complexity, McCarthy says. A small, basic quarterboard runs around $600, while elaborate pieces can cost $3,000-$4,000.
On Martha’s Vineyard, JP Uranker hand carves a variety of signs, including quarterboards. “A sign is a piece of artwork families are going to have for years to come,” he says. “They are family heirlooms.” Eagles and quarterboards are his biggest sellers.
Uranker, who has been carving for about 50 years, makes all his signs out of mahogany, which he considers more durable than pine, and finishes them with a marine-based paint made in Europe. He uses 23-karat Italian gold leaf, which he says has “a nice shine and presentation.” One of his signature touches is brass keyhole slots on the back of the piece, so there are no holes going through the sign.
On the Vineyard, people tend to opt for traditional designs on the carved ends, such as pineapple fronds, but the sky’s the limit, Uranker says. “As big as someone’s imagination is, that’s what I can put on the end of a quarterboard.”
In Chatham, Bob Lacy has been creating quarterboards at Chatham Sign Shop for 30 years. Like McCarthy and Uranker, he started out carving by hand. But in the early 2000s, he and many other carvers began using a CNC (computerized numerical control) router for lettering, though some of the ornamental end pieces are still hand carved.
Creating quarterboards with machines isn’t necessarily less expensive, Lacy says, because the machines are very costly. But it does allow the shop to produce a greater volume, and it’s much less punishing on the carvers, who are vulnerable to such problems as carpal tunnel syndrome.
Around the same time that Lacy switched to the CNC router, he began working with alternatives to forest wood. “Wood has one purpose, and that is to transport water up the trunk of the tree and into the leaves,” he says. “Composites allow us to use a material that won’t absorb water and holds paint better.”
Some things have not changed. Many templates are based on historical quarterboards; scallop shells are still the most popular motif; black and gold remain the first choice for lettering; and Lacy still uses 23-karat gold pounded into leaf for accents. “Gold leaf outlasts any other kind of finish,” he says. “I’ve seen the old boards rot away, but the gold stays.” Gold-leaf-accented quarterboards created at Chatham Sign begin around $365, Lacy says, and can run up to $2,000 or more depending on size.
Paul White, of Paul White Woodcarving in East Sandwich, started making quarterboards as a hobby in the mid-1960s. Some 50 years later, he specializes in a variety of hand-carved items, including signs, figureheads and various marine creatures. His signature eagles, created with chisels and mallets and finished with 23-karat gold, are displayed in homes and businesses around the world.
White has been teaching almost as long as he’s been carving. “Half the people on the Cape who carve, either I taught or people I taught have taught them,” he says. His two-day basic carving course gives beginners a strong overview, but success is all about practice.
Among White’s more unusual commissions are a gorilla, a horned creature from the children’s book “Where the Wild Things Are,” and a 6-foot grape Popsicle. What does he most like to carve? “Something new and different.”
Seaport Shutter Company, based in Brewster and Chatham, recently launched The Sign Shop, specializing in custom signs, many in the quarterboard tradition and style, says Lauren Huard, director of sales. Huard’s father, Peter Malone, founded the company in 1992 and remains very involved on the creative side, Huard says. “Our business is all about design, style and color. My father has personal style, flair, spirit and a very creative eye—he helps make our products come to life.”
Seaport crafts signs primarily in mahogany and finishes them with five coats of paint or a marine-grade stain or varnish. “We find that mahogany does well in the elements,” Huard says, “and it has a natural, traditional, timeless look.” While signs are carved by machine, a team of artists hand letters each sign, and finishes can be applied by hand. Prices begin around $395 for a small (24-inch) quarterboard.
In addition to its large selection of carvings and appliques, the company offers all custom designs too. Huard describes a sign created for a Los Angeles family with a summer home in Orleans, with the slogan “Coast to Coast” flanked by appliques of California and Massachusetts.
Most quarterboard artists have tales to tell about the clever wordplay that finds its way into their custom creations. Lacy recounts the story of a man and woman who had each just gotten divorced, and were about to wed one another. For their slogan they chose “Eat, drink, and remarry.” And there’s no lack of double entendre on Nantucket, says McCarthy. He has made several quarterboards for the Frazier family, including one that says “Deuce Coop” for Libby Frazier, who keeps two chickens as pets. “And because the Beach Boys are my husband’s favorite,” Frazier notes. Another memorable sign is a quarterboard McCarthy made for a surgeon that says simply “Suture Self.”